Gate, Globe, And Check Valves
Inventory
First Distributors Offers a wide array of gate, globe, and check valves in carbon steel, stainless steel, and even exotic alloys. With sizes starting at ¼”, and pressure classes ranging from 150# - 2500#, we can supply gates, globes, and checks to meet whatever requirements your project has.
SIZE RANGE: | ¼” – any size |
GATE: | Wedge, Knife |
GLOBE: | T-pattern, Y-pattern, 90-pattern |
CHECK: | Swing, Wafer, Piston |
PRESSURE CLASS: | 150# - 4500# |
END CONNECTIONS: | Flanged, Threaded, Socket Weld, THD x SW, Butt Weld |
PORT: | Full Port, Reduced Port |
BONNET: | Bolted, Welded |
MATERIAL: | Carbon steel, stainless steel, exotic alloys |
TRIM: | API trim #’s 1-18 |
Materials Available
The two most common specs for carbon steel valves are A105 and A216. If you need one or the other, be sure to specify. A105 is the spec for forged carbon steel while A216 is the spec for cast carbon steel. See below for more detail on how cast and forged steel are created. Generally, forged steel is stronger than cast steel. Also, it is important to note the different sizes ranges that are available in both forged and cast steel. While cast steel valves can be made to meet virtually any size requirement for your application, forged steel valves are only available up through 4” due to the sheer energy that is required to forge carbon steel. Casting is a much more viable and speedy alternative when dealing with bigger valves. If you’re dealing with a smaller high-pressure application, then maybe consider forged steel.
Trims Available
The trim refers to the material that makes up the internal elements of a valve. Please see First Distributor’s handy trim chart for assistance in deciding which trim you need for your valve.
TRIM NO 1 | SEAT | WEDGE | STEM |
---|---|---|---|
1 | 13 CHROME | 13 CHROME | 13 CHROME |
2 | 304 | 304 | A76 304 |
3 | 310 | 310 | A276 310 |
4 | HARD 410 | HARD 410 | 410 |
5 | 13 CHROME W/STELLITE 6 FACING | 13 CHROME W/STELLITE 6 FACING | A276 410 OR 420 |
5a | NI-CR | NI-CR | 410 |
6 | 13 CHROME W/30% MIN NICKEL FACING | NI-CR | A276 410 OR 420 |
7 | HARD 410 | HARD 410 | 410 |
8 | 13 CHROME W/STELLITE 6 FACING | 13 CHROME | A276 410 OR 420 |
8A | NI-CR | 410 | 410 |
9 | MONEL | MONEL | MONEL |
10 | 316 | 316 | A276 316 |
11 | MONEL W/STELLITE 6 FACING | MONEL | MONEL |
12 | 316 W/STELLITE 6 FACING | A276 316 | A276 316 |
13 | ALLOY 20 | ALLOY 20 | B473 |
14 | ALLOY 20 W/STELLITE 6 FACING | ALLOY 20 | B473 |
15 | 304 W/STELLITE 6 FACING | 304 W/STELLITE 6 FACING | A276 304 |
16 | 316 W/STELLITE 6 FACING 347 | 316 W/STELLITE 6 FACING 347 | A276 316 |
17 | 347 | 347 | A276 347 |
18 | ALLOY 20 W/STELLITE 6 FACING | ALLOY 20 W/STELLITE 6 FACING | ALLOY 20 |
A Guide To Gate, Globe, And Check Valves
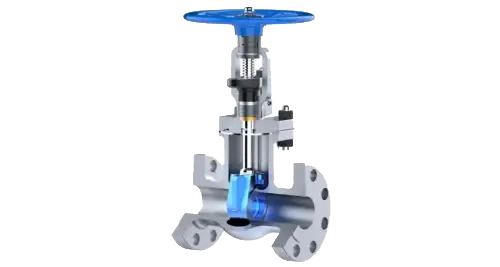
Gate
Knife Gate
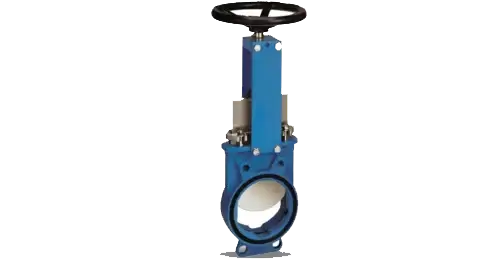
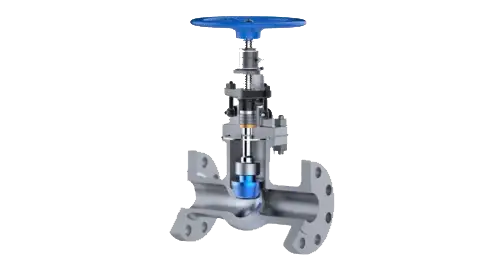
Globe
90-degree Pattern (angle)
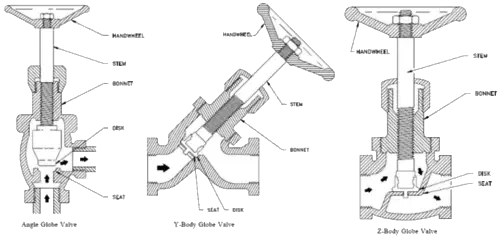
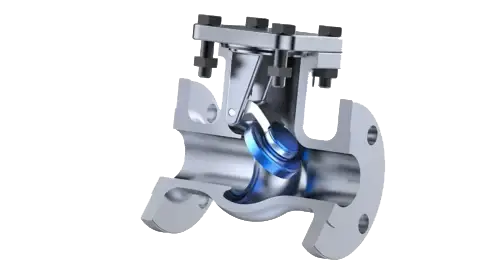
Check
Wafer Check
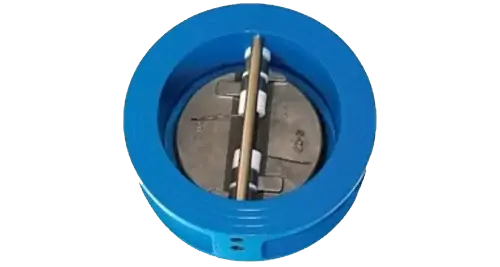
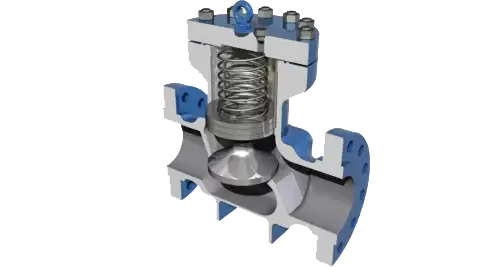
Piston Check
T-pattern Globe (z-body)
Y-pattern Globe (y-body)
Swing Check
Wedge Gate
Full Port Vs. Reduced Port
Gates, globes, and check valves can all be either full port or reduced port. However, most people do not specify a port type when ordering these valves. The standard is a reduced port. Full port valves have no restriction of flow from the original pipe diameter. If the pipe diameter of the valve is 2”, then a full port valve will be 2” wide all the way through. They will maintain a consistent flow rate. The opening in a reduced port valve is smaller than its designated pipe diameter. Reduced port valves are typically less expensive than full port valves and are a good option for use in applications that will be transferring liquids only. If your application will be transferring both liquids and solids, then it might be best to go with a full port valve to avoid clogging the application.
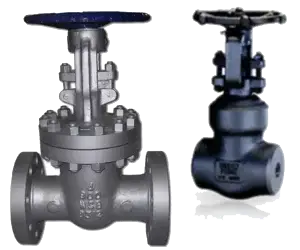